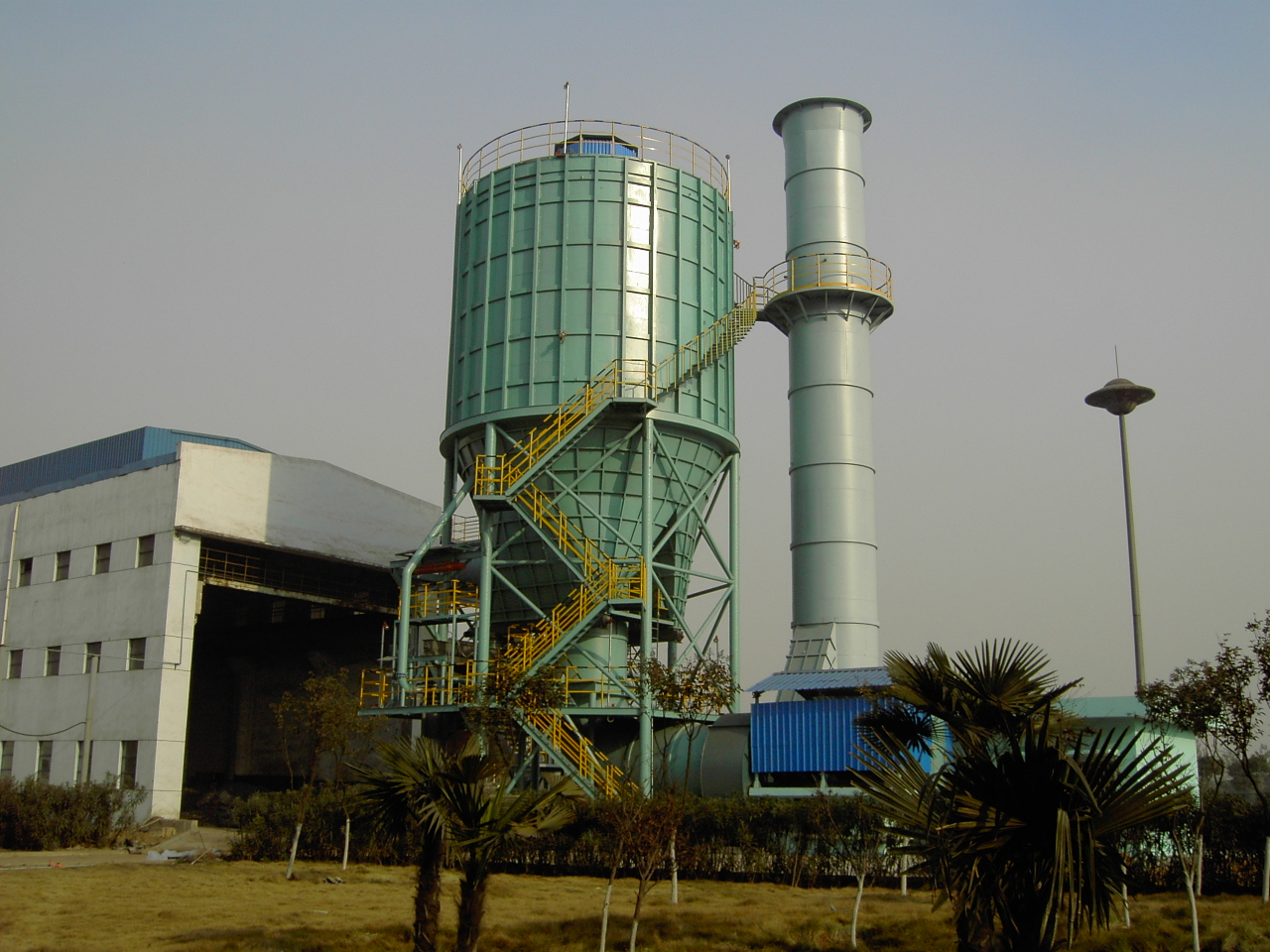
This project provides dust and flue gas capture and ultra-low emission control for the entire steelmaking workshop for the newly built 2 electric furnaces and supporting refining, continuous casting and other equipment; At the same time, a quench boiler is equipped for the high temperature flue gas discharged from the electric furnace smelting process, which not only meets the requirements of rapid cooling of dioxins, but also achieves efficient waste heat recovery of the flue gas. The generated steam is used for steam turbine generator units (15MW), greatly reducing the operating costs of the enterprise.
This project includes 4 * 100 steel continuous feeding electric furnace dust removal system, as well as corresponding refining dust removal systems such as LF furnace, continuous casting, and feeding systems. The electric furnace dust removal system adopts a combination mode of "primary flue exhaust inside the furnace+secondary flue exhaust outside the furnace+third flue exhaust on the roof" for flue gas and dust control. The capture hood meets the requirements of a capture rate greater than 98% and a dust emission concentration of ≤ 10mg/Nm3.
This project provides dust and flue gas capture and ultra-low emission control for the entire steelmaking workshop for the newly built 2 electric furnaces and refining device, continuous casting and other equipment; At the same time, a quench boiler is equipped for the high temperature flue gas discharged from the electric furnace smelting process, which not only meets the requirements of rapid cooling of dioxins, but also achieves efficient waste heat recovery of the flue gas. The generated steam is used for the steam turbine generator unit (12MW), greatly reducing the direct operating cost of the enterprise.