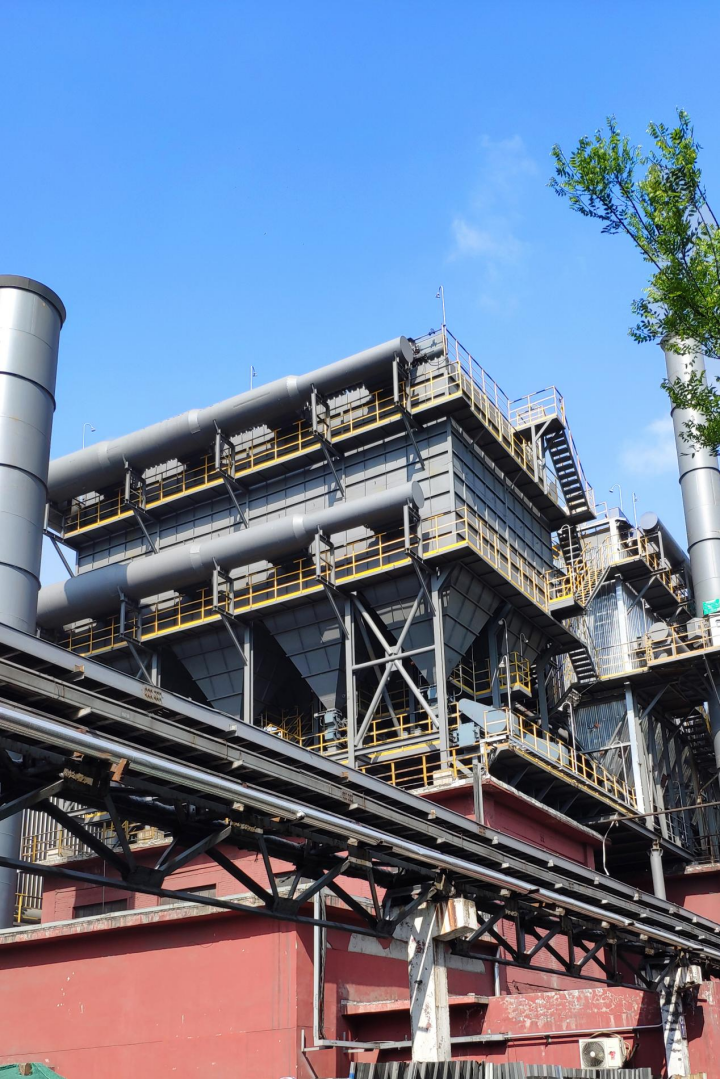
The project adopts a selective catalytic reduction (SCR) denitration device, with a denitration efficiency higher than 90% for coal fired boilers (with a catalyst arrangement of 3+1) under the conditions of designed and verified coal types, maximum continuous evaporation capacity (BMCR) of boilers, and 100% gas processing.
In order to actively meet national environmental protection requirements, Shanxi Coking Company has invested in the construction of 1 #, 4 #, and 5 # coke oven flue gas desulfurization and denitration devices, which can meet the ultra-low emission requirements of the Linfen region for coke oven pollutants. The coke oven adopts a system configuration of SDS dry desulfurization+bag dust removal+denitration system. Except modification of existing part, a new set of flue gas desulfurization and dust removal system and corresponding supporting facilities was built. The system adopts a technological process of "baking soda dry desulfurization (SDS)+bag dust removal+low-temperature denitration process (SCR)+waste heat recovery+induced draft fan" to ensure that the concentration of particulate matter (standard and dry basis) is ≤ 10mg/Nm3, sulfur dioxide (standard and dry basis) is ≤ 30mg/Nm3, and nitrogen oxides (standard and dry basis) is ≤ 100mg/Nm3.
In order to actively meet national environmental protection requirements, Shanxi Coking Company has invested in the construction of 1 #, 4 #, and 5 # coke oven flue gas desulfurization and denitration devices, which can meet the ultra-low emission requirements of the Linfen region for coke oven pollutants. The coke oven adopts a system configuration of SDS dry desulfurization+bag dust removal+denitration system. Except modification of existing part, a new set of flue gas desulfurization and dust removal system and corresponding supporting facilities was built. The system adopts a technological process of "baking soda dry desulfurization (SDS)+bag dust removal+low-temperature denitration process (SCR)+waste heat recovery+induced draft fan" to ensure that the concentration of particulate matter (standard and dry basis) is ≤ 10mg/Nm3, sulfur dioxide (standard and dry basis) is ≤ 30mg/Nm3, and nitrogen oxides (standard and dry basis) is ≤ 100mg/Nm3.
The explosion-proof pulse bag dust collector is used to treat the dust generated during the feeding and transportation process of the blast furnace. After treatment, the emission concentration is ≤ 10mg/m3. The dust is transported pneumatically and the entire process is sealed.
This project is aimed at the dust removal system modification of the 75tconsteel continuous feeding electric furnace of Guixin Third Refinery. The electric furnace dust removal system uses flue gas to be led out through a horizontal feeding channel, connected to the settling chamber and quench tower for treatment, and then fed into the dust collector, meeting the environmental protection needs after improving the working conditions.
In order to meet the requirements of implementing ultra-low emission standards in 2022 and increasing the operation load in the later stage of the plant, Jilin Jianlong Iron and Steel Company built a desulfurization and WESP system for two 10m2 shaft furnaces to meet the full load operation requirements of the two furnaces, and to reduce the emission concentration of flue and dust particles in the treated flue gas to less than 10 mg/Nm3 and the emission concentration of SO2 to less than 35 mg/Nm3.